1. 概述
铝基碳化硅(sicp/al)复合材料是轻质高强高尺寸稳定性的结构功能材料,其增强体的含量不同,材料性能和功能也具有较大区别 [1] ;当前航空航天高性能精密结构件向着极端环境、极端轻量化、高度集成化的趋势发展,需要在有限的设计空间内实现结构功能一体化的集成,以提高器件的兼容性和环境适用性 [2] 。
sicp/al复合材料恰好能够满足航空航天精密结构件性能的同时实现梯度变化的设计需求,不同体分材料间的界面仅有碳化硅粒度和含量的不同,不存在异种材料结合界面不相容的本质性缺陷问题,能够在功能部分采用高体积分数sicp/al复合材料,主要利用其较低的热膨胀性能,而在结构端使用具有良好力学性能的中低体分sicp/al复合材料,中间过渡部分则选用介于二者之间合适体分的sicp/al复合材料与两端形成良好结合,在达到结构功能整体设计的同时使整个构件具有优异性能 [3] 。
本文以sicp/al复合材料不同梯度结构为研究对象,利用ansys workbench软件中的瞬态动力学分析模块,按照预设的实验测试条件,添加梯度sicp/al复合材料所受的约束和载荷,对其进行抗弯强度测试状态下的力学性能模拟分析,得到等效应力、等效应变以及总形变等结果,对材料性能和梯度结构进行仿真计算模拟,建立设计思路和研究方法,达到结构功能一体化设计构想,并作为后续相关材料的研究基础 [4] 。
2. 梯度sicp/al复合材料概述
(一) 制备方法
本文中的梯度sicp/al复合材料的制备技术路线分两部分,首先通过凝胶注模法制备并烧结成型梯度孔隙率的碳化硅预制件,然后对其进行真空压力渗铝近净成形铝基碳化硅梯度材料及器件 [5] 。
凝胶注模制备时,根据各梯度层的材料性能需求,配置几组不同碳化硅颗粒级配的凝胶混合体,以把控各梯度层的增强体体积分数;注模后,通过碳化硅颗粒的短距离沉降,使分层界面消失,实现梯度界面的自然过渡。在真空压力渗铝时,近净成形工艺可以从结构上缩短铝液的渗透尺寸,使结构件致密度高、性能均匀,同时能够减少结构件的加工量,降低加工难度和加工成本 [6] 。
所制备的梯度sicp/al复合材料样件如下图1。
从左至右材料体分由低到高分布
. the cross-section of gradient sicp/al composite sample
图1. 梯度sicp/al复合材料样件截面图
(二) 材料表征
为进一步观察梯度sicp/al复合材料中各部分界面结合的情况,根据所制备梯度sicp/al复合材料样件的微观结构表征结果(图2),对材料可能出现的缺陷问题进行改进优化。
从左至右材料体分由低到高分布
. material volume fraction distribution from left to right from low to high
图2. 梯度sicp/al复合材料界面sem镜下照片
由图2可见,左侧部分为小粒径sic的38%.volsicp/al复合材料部分,中间部位采用50%.volsicp/al复合材料作为过渡部分,右侧部分为大粒径sic的63%.volsicp/al复合材料部分,整个梯度sicp/al复合材料的过渡区域结合均匀紧密,没有明显孔洞、界面分界缺陷,可见采用凝胶注模 真空压力渗铝的工艺路线可行,能够制备出组织致密度高、界面结合较好的梯度铝基碳化硅复合材料。
(三) 力学性能测试
通过对梯度sicp/al复合材料进行4种不同分布结构设计后,分别对单层材料及4种梯度材料进行相同条件下的抗弯强度测试,以体现不同结构材料间的力学性能差异(表1)。
. related mechanical properties of gradient sicp/al composites
表1. 梯度sicp/al复合材料相关力学性能
由上表1可以看出,上–下递减梯度结构的抗弯强度最高,为651 mpa,左–右结构的抗弯强度为507 mpa,与50%.vol材料强度接近;而前–后结构和上–下递增梯度结构的抗弯强度反而远低于强度最低的63%.vol材料。由图2 sem照片的组织状态可以排除界面缺陷可能导致材料力学性能降低的因素;同时,综合上述结果也可以发现,通过一般的材料表征及测试方法无法较好的体现梯度sicp/al复合材料的层间应力分布等情况,因此通过采用专业模拟软件对梯度铝基复合材料进行抗弯强度测试条件下的模拟仿真,以期解释不同结构间力学性能产生差异的原因 [7] 。
3. 梯度sicp/al复合材料样件三维模型
通过solid works软件对梯度sicp/al复合材料样件进行建模后导入ansys workbench软件(图3),样件长50 mm,宽6 mm,整体厚度6 mm,体积1.8 cm3,材料平均密度2.95 g/cm3。样件的基本结构参数为:三种体分材料各占三分之一,下部两支点跨距均为25 mm,上部压头位于材料中央。
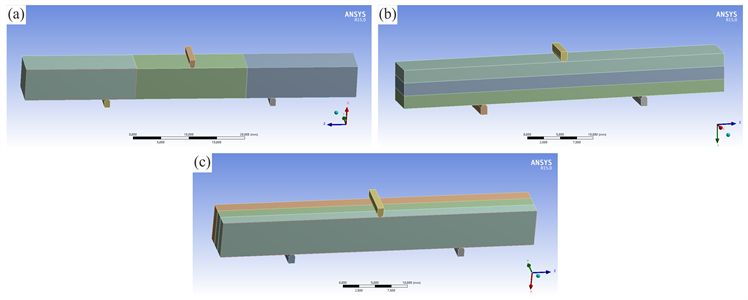
. different structural of gradient sicp/al composite sample schematic diagram; (a) left-right structural; (b) upper-lower structural; (c) front-back structural
图3. 不同结构梯度sicp/al复合材料样件示意图;(a) 左–右结构;(b) 上–下结构;(c) 前–后结构
为方便进行模拟仿真和载荷施加且不影响整体结构和施力,在每种样件上部施力部位和下部的两个支撑部位共添加三根长6 mm,宽1 mm,厚1.58 mm,密度为7.85 g/cm3的材质为结构钢的条形结构,以模拟抗弯强度测试时样件放置情况。
(一) 建立梯度sicp/al复合材料样件有限元模型
首先将材料属性设置为铝基,然后将下表2中单层sicp/al复合材料相关力学属性输入ansys workbench材料属性设置界面,材料抗弯强度数据为单层sicp/al复合材料的抗弯强度实测结果。其次梯度sicp/al复合材料样件采用六面体网格划分法,有限元网格划分单元尺寸0.3 mm,单元数85,928,节点数365,278。
. related mechanical properties of sicp/al composites
表2. sicp/al复合材料相关力学性能
(二) 瞬态动力学分析
在transient structural瞬态动力学分析前根据梯度sicp/al复合材料样件的测试情况,对下部2个支脚施加fixed support固定约束,对上部的1个主要受力区域施加force受力(图4);再通过对4种不同结构形式的梯度sicp/al复合材料样件所受应力、应变和总变形进行求解,得到equivalent stress等效应力、equivalent elastic strain等效应变及total deformation总变形量相关数据。
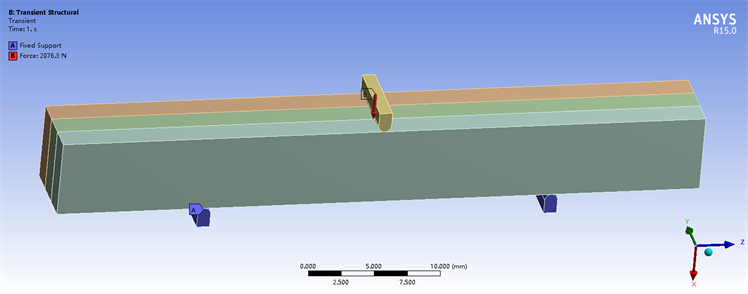
. constraints and stress diagrams of gradient sicp/al composites
图4. 梯度sicp/al复合材料约束及受力图
为准确得到模拟时对4种梯度sicp/al复合材料所施加的载荷受力,由于实际测试时的样件尺寸各有不同,最大载荷需对应材料建模尺寸进行相应换算,即模拟施加载荷 = [最大载荷/(实际厚度*实际宽度)]*(建模厚度*建模宽度),其中建模厚度和建模宽度均为6 mm (表3) [8] 。
在抗弯测试时,随着上部压头缓慢下降对试样施力,通常是试样背面先出现裂痕并发生整体断裂(图5),此时仪器记录断裂瞬间的最大载荷并计算出抗弯强度,而下部的跨距支架则对试样主要产生较大的压应力,因此在模拟时主要观测上部压头接触部位所受应力及梯度界面的应力和应变情况。
. related mechanical properties of gradient sicp/al composites
表3. 梯度sicp/al复合材料载荷受力
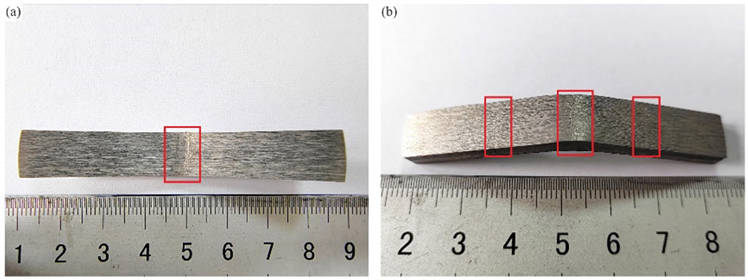
. the actual situation of flexural strength test of flexural specimens; (a) frontal indentation; (b) back indentation and fracture
图5. 抗弯试样抗弯强度测试实际情况;(a) 正面压痕;(b) 背面压痕及断裂
4. 梯度sicp/al复合材料样件三维模型模拟结果分析
(一) 左–右梯度结构
由图6左–右梯度结构的模拟结果图可以看出,上部压头接触主体为50%.volsicp/al部分,且与两侧梯度界面相距较远,因此更多的体现了50%.vol材料自身性能;模拟数据显示压头接触中间部位材料受应力535 mpa,大于50%.volsicp/al材料本身的抗弯强度509 mpa,大于左–右梯度sicp/al材料的抗弯强度507 mpa,可见对于此梯度结构来说,梯度界面的应力集中对材料整体强度影响不大,最大形变
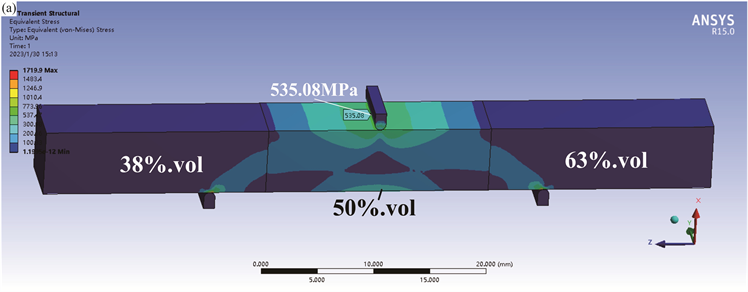
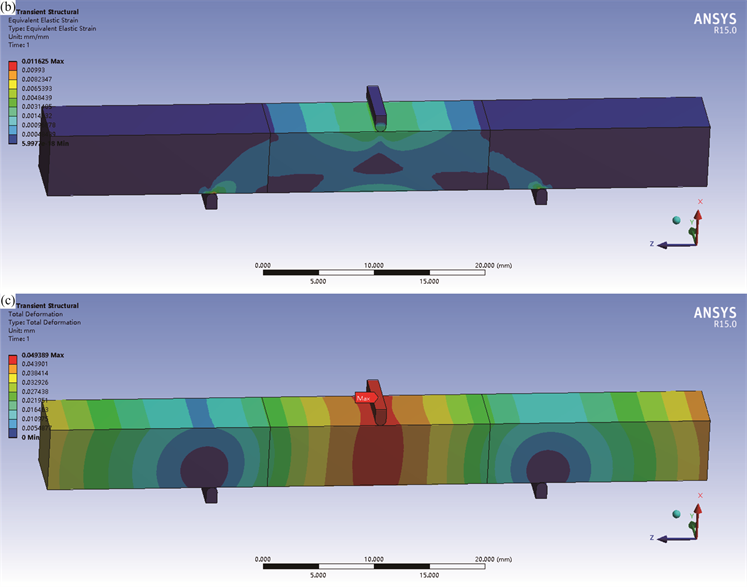
. left-right gradient transient structural simulation results; (a) equivalent stress; (b) equivalent strain; (c) total deformation
图6. 左–右梯度结构瞬态动力学模拟结果;(a) 等效应力;(b) 等效应变;(c) 总形变量
部位在试样中央断裂区域。图6(b)则显示等效应变分布趋势与应力分布趋势基本一致,说明根据弹性模量相关定义,在受相同应力时的弹性模量小的部分等效应变的数值和影响范围较大,形变量则相对较小。
(二) 上–下梯度形式
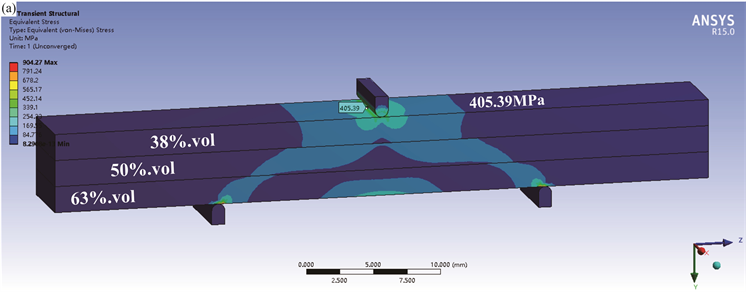
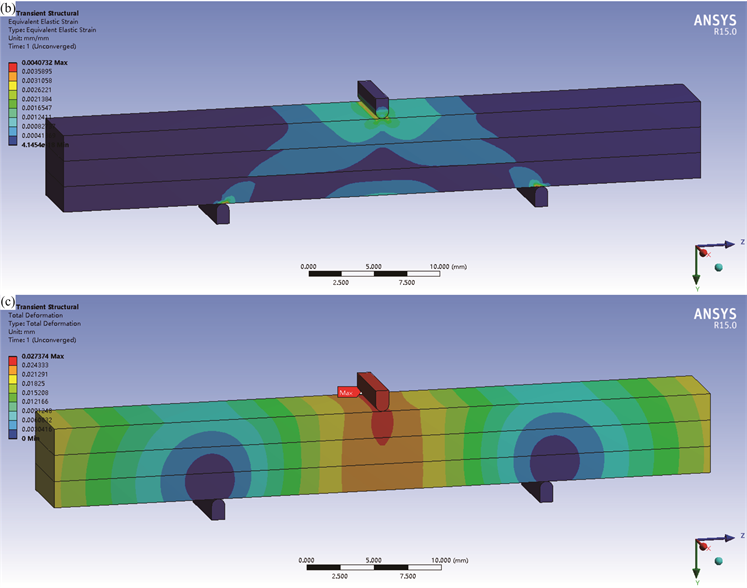
. upper-lower increasing gradient transient structural simulation results; (a) equivalent stress; (b) equivalent strain; (c) total deformation
图7. 上–下递增梯度结构瞬态动力学模拟结果;(a) 等效应力;(b) 等效应变;(c) 总形变量
1) 上–下递增梯度结构
由图7上–下递增梯度结构的模拟结果图可以看出,上部压头所接触部位主要为38%.vol部分,图中(a)显示压头接触中间部位材料受应力405 mpa,远小于各体分sicp/al材料自身的抗弯强度(572 mpa, 509 mpa, 484 mpa),较大于上–下递增梯度sicp/al材料平均抗弯强度393 mpa,可见梯度界面的应力集中对梯度材料整体性能影响较大,最大形变部位在试样中央受力断裂处。
其中,38%.volsicp/al由于弹性模量较小(145 gpa),受到同样的应力时,产生的应变和形变量相对较大,继续受力情况下,应变和变形量快速向下传递,而最下层63%.volsicp/al的弹性模量(225 gpa)与最上层差距较大,在同样的应变或者变形量的时候受应力大,更容易发生应力集中,而其材料强度最低,无法承受与最上层相同的应变和形变量,因此递增梯度结构材料的力学性能低于单层材料,相比单一体分材料更容易发生断裂。
2) 上–下递减梯度结构
由图8 上–下递减梯度结构的模拟结果图可以看出,上部压头所接触部位主要为63%.vol部分,图中(a)显示压头接触中间部位材料受应力729 mpa,远大于各体分sicp/al材料自身的抗弯强度(572 mpa, 509 mpa, 484 mpa),大于该梯度结构sicp/al材料抗弯强度651 mpa,可见梯度界面的应力分布对材料力学性能影响较大,最大形变部位在试样中央断裂处。

. upper-lower decreasing gradient transient structural simulation results; (a) equivalent stress; (b) equivalent strain; (c) total deformation
图8. 上–下递减梯度结构瞬态动力学模拟结果;(a) 等效应力;(b) 等效应变;(c) 总形变量
其中,虽然位于最上层的63%.volsicp/al的抗弯强度相对较低,但其弹性模量(225 gpa)较大,载荷施加时所产生的应变和形变量较小,在应力向下传递过程中,对传递的应变和形变具有良好的吸收作用,传递给下部38%.volsicp/al材料的等效应力和变形量会相对延迟,而由于下部50%.vol~38%.volsicp/al材料的强度逐渐较高,断裂应变量较大,能够有效支撑上部63%.volsicp/al材料的“塌陷”,能够起到缓解因受力而产生断裂的趋势,因此上–下递减梯度结构在力学性能方面产生了良好的“1 1 1 > 3”的梯度材料受力效果。
(三) 前–后梯度形式结构

. forward-backward gradient transient structural simulation results; (a) equivalent stress; (b) equivalent strain; (c) total deformation
图9. 前–后梯度结构瞬态动力学模拟结果;(a) 等效应力;(b) 等效应变;(c) 总形变量
由图9前–后梯度结构的模拟结果图可以看出,上部压头同时均等接触三种体分sicp/al材料,因此图中(b)显示接触面的三种体分材料的等效应变分布趋势相同;而图中(a)则说明各层材料由于自身性能差异,在受相同载荷时的应力分布趋势不同,在梯度层间产生了明显的应力集中现象。
由于上部压头同时对三层梯度部分施力,因此各层应变分布趋势相等,但63%.volsicp/al材料弹性模量较大,在产生相同应变时其等效应力相对较大,而其材料强度最低,63%.volsicp/al材料部分会引起应力集中,当超过最大载荷时会从结构背部63%.vol材料部分开始断裂,然后裂纹向前部和其他部位引起试样断裂,相当于引发了“短板效应”,也是前–后梯度结构抗弯强度较低的原因。
5. 结论
1) 本文制备了一种碳化硅体积占比为38%.vol~63%.vol的梯度sicp/al复合材料,并表征其微观组织和测试其力学性能,结果表明该梯度材料组织致密、界面结合良好。
2) 本文利用ansys workbench软件对左–右梯度、上–下递增梯度、上–下递减梯度、前–后梯度等4种梯度结构模式进行瞬态动力学分析,得到不同梯度结构的模拟数据与其相应的实测数据的变化规律一致。
3) 本文结合实际的检测数据与模拟计算得出的应力–应变等力学结果,分析了不同梯度结构sicp/al复合材料的力学行为和可能引起其断裂失效的受力模式,为设计和使用梯度结构sicp/al复合材料提供理论参考依据。