1. 概述
sicp/al复合材料表现出轻质高强、高热导率和低热膨胀系数等优异性能,既是先进的电子封装材料,也是先进的结构材料。但在材料的加工过程中,常常出现加工精度和加工效率难以共同保证的情况,且高硬度sic颗粒–铝基体–加工工具之间复杂的相互作用会导致颗粒断裂、界面脱粘和划痕等表面损伤,在很大程度上制约了sicp/al复合材料的发展与应用(如图1)。
近年来,大量研究人员从不同角度对sicp/al复合材料的加工技术进行了深入研究,其中传统加工方式包括车削、铣、钻、磨等,非传统加工方式例如超声振动加工、电化学加工、电火花加工和激光辅助加工等,而在电场与超声场相复合的加工技术及其对材料加工性能的深入分析较少,且对于中高体积分数(40~70 vol.%) sicp/al复合材料的加工研究较少,不足以指导sicp/al复合材料的电–超声等复合加工相关应用。
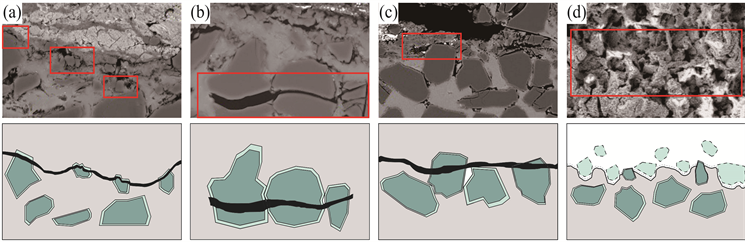
. sicp/al composite defect type diagram [1] ; (a) interface debonding; (b) fracture of sic particles; (c) al matrix fracture; (d) corrosion of al matrix
图1. sicp/al复合材料缺陷类型示意图 [1] ;(a) 界面脱粘;(b) sic颗粒断裂;(c) al基体断裂;(d) al基体腐蚀
图2介绍了sicp/al复合材料体积分数由低到高的不同特性、重要应用以及具有优良应用效果的复合加工方式。
其中,航空重要承重结构件和导航等领域因其使用环境复杂、负载高、承力大等特点,一般使用具有高强度和高韧性的10%~30 vol.% sicp/al替代合金材料,并且为了轻量化等需求,其往往设计有需要大余量去除的镂空结构;另一方面,低体分sicp/al复合材料更多的显现为铝基体的性能,在热处理强化前相对较易加工,加工方式选择范围广,但材料受残余应力影响较大,需要通过去应力处理减少构件的变形。对于光机结构件、光学反射镜等精密仪器,则需要在薄壁、异形等复杂结构部位保证其加工精度和表面质量,因此具有高尺寸稳定性的40~55 vol.% sicp/al常用于制备整体构件以代替焊接结构,使其能够经受长时振动和冲击条件下的疲劳环境。作为第三代封装材料,高体分(60%~70 vol.%) sicp/al复合材料既能够用作微组装散热载体,也能作为散热基板和封装盒体在多种严峻环境下保障大功率电子元器件的高效工作。但由于其增强体含量较高,电加工困难,且在加工台阶、沟槽等微结构和螺纹孔等难加工部位时容易出现崩裂等缺陷。
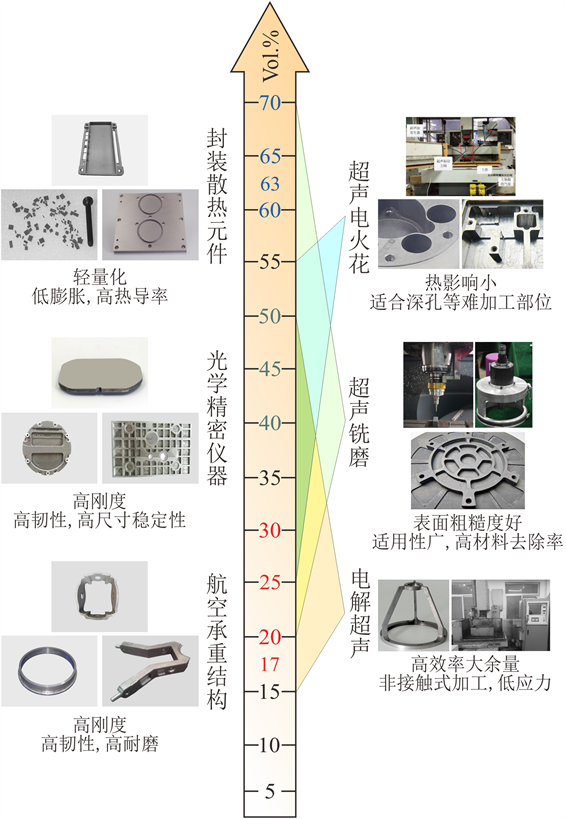
. characteristics of sicp/al composites and composite processing applications [1] [2]
图2. sicp/al复合材料及复合加工应用特点 [1] [2]
总之,复合材料的性能受sic含量的影响最为显著,在对不同体分、不同应用、不同结构要求的sicp/al复合材料进行加工时,需要在不同加工阶段选取合适高效高质量的加工方式。因此,本文通过对现有sicp/al复合材料复合加工技术进行研究,分析对比主要加工技术的长处,力求为sicp/al复合材料复合加工技术的创新应用做些有意义的工作。
2. sicp/al复合材料电加工技术
表1列举了基于sicp/al复合材料的三种常用电加工技术。
. common electrical processing technology of sicp/al composites
表1. sicp/al复合材料常用电加工技术 [3] [4] [5]
其中,电火花加工包括电火花线切割和电火花成形加工,分别用于型腔和异形不通孔加工;电弧放电加工是近年来兴起的加工方式,进行开敞式叶盘 [6] [7] 、框架结构、离心叶轮 [8] 、机匣等零部件的加工;相比于以上两种加工方式,电解加工的适用范围更广,如炮管膛线 [9] [10] 、叶轮叶片、异型孔及异型零件 [11] [12] 、倒角和去毛刺等加工。
(一) 电火花加工
采用电火花加工技术对sicp/al复合材料进行加工时,将电火花加工原理与材料自身的结构特点相结合,利用加工基体金属时放电产生的能量使得材料剥落,甚至是sic的熔化和气化(图3)。
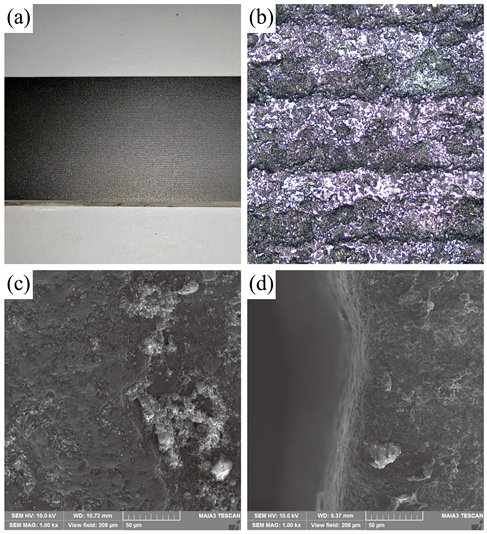
. the surface morphology of sicp/al processed by electrical discharge wire-cutting; (a) working surface; (b) microscope photo; (c) micro-characteristics of working surface; (d) micro-characteristics of cross-section
图3. 电火花线切割加工sicp/al复合材料表面形貌;(a) 加工面;(b) 显微镜下照片;(c) 加工表面微观特征;(d) 加工截面微观特征
图3为电火花线切割加工表面形貌照片,表面较平整,但有具明显走丝方向变换产生的等距条纹,表面粗糙度约为ra3.2;sem照片显示电火花线切割面出现轻微放电弧坑,截面无可见裂纹等缺陷,热影响区不明显 [13] 。
唐霖等 [14] 以10 vol.% sicp/al为对象研究了电火花加工单脉冲及多脉冲放电状态下的温度场分布,并进行了内、外冲液对比试验及参数优化,得出电极相对损耗率与加工深度、材料去除率和冲液压力成正比,且内冲液电极相比外冲液电极相对损耗大。于朋等 [15] 对35 vol.% sicp/2024al进行电火花深小孔加工,当采用螺旋电极时材料去除率和孔壁质量明显高于普通圆柱电极,热应力大小和微裂纹宽度深度与放电能量密度有关。刘宇等 [16] 选择zl101a基体的65 vol.% sicp/al复合材料在自搭建的电火花加工实验台上进行实验,验证得出铜钨合金和紫铜电极材料对材料去除率影响不大,且前者损耗远小于后者,最终得到3.842 mm3/min的材料去除率。
总的来说,利用电火花加工sicp/al复合材料时,由于sic颗粒的屏蔽效应,材料的去除效率较低、工件表面质量不高,且随着中高体分材料中sic增强相体积分数的增加,加工变得越来越困难,因此单一的电火花加工已不再适合sicp/al复合材料高效、高精度复杂结构的加工要求。
(二) 电弧放电加工
电弧放电加工技术相比电火花加工具有更高能量密度,其原理是通过电极运动和内冲液作用切断电极与工件之间产生的电弧柱而形成断弧作用,在可控范围内通过非稳态的电弧将加工部位熔融,再利用内外冲液的流体将材料熔融部分快速去除并冷却工件表面 [17] (图4,图5)。
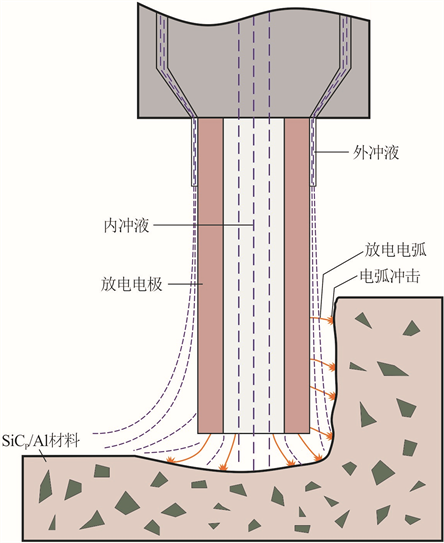
. arc machining principle diagram
图4. 电弧加工原理示意图 [18]
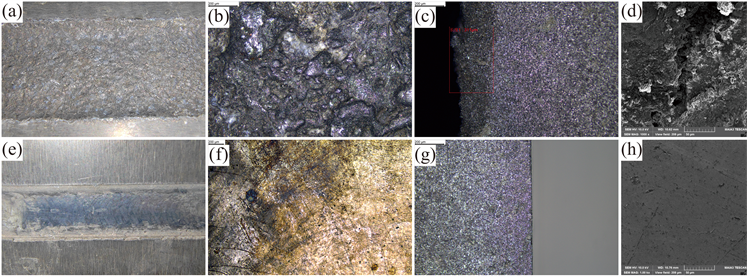
. macro and micro photos of arc machining; (a) high power arc machining surface; (b) the microscopic characteristics of the machined surface; (c) cross-sectional characteristics under the microscope; (d) sem photos of machined surface; (e) low power arc machining surface; (f) the microscopic characteristics of the machined surface; (g) cross-sectional characteristics under the microscope; (h) sem photos of machined surface
图5. 电弧加工宏微观照片;(a) 高功率电弧加工面;(b) 加工表面显微特征;(c) 显微镜下截面特征;(d) 加工表面sem照片;(e) 低功率电弧加工面;(f) 加工表面显微特征;(g) 显微镜下截面特征;(h) 加工表面sem照片
. characteristics of processing recast layer and heat-affected layer
表2. 电弧加工再铸层和热影响层特征
综合图5和上表2可以看出,高功率电弧加工表面瘤状产物最多,严重影响了表面粗糙度,且热影响深度达273 μm,表明随着电弧加工放电功率(加工去除率)的增加,表面反应产物越来越多,表面粗糙度及加工硬化程度就会越高 [19] [20] ,因此需要对放电功率进行一定范围内的控制,使其在高效大余量去除的同时兼顾一定的加工质量;当采用低功率电弧加工时,其热影响深度较浅,为20 μm左右,此时各项指标与数铣加工相当,加工表面质量较好、加工精度相对较高。
陈吉朋等 [21] 研究了高速电弧放电作用力在不同参数下的特性,发现提高脉冲宽度能够有效提高加工效率,而放电作用与峰值电流无明显对应关系,但受开路电压影响较大,且作用力主要出现在放电初期,对材料的抛出不起主要作用。上海交通大学 [22] 提出的基于复合断弧机制的电弧轮廓切割加工,在加工“天宫二号”20 vol.% sicp/al支架时,将整个支架结构的切割加工时间降低到2 h以内,平均切割面效率可达550 m2/min,远高于电火花加工。
需要注意的是,电子、离子在电场中的运动和电弧等离子体的形成和扩张等效应依然会产生类似于切削应力的作用,因此在加工某些sicp/al薄壁结构时需要尽可能降低电源参数。
(三) 电解加工
电解加工属于电化学加工(ecm),其原理是将一定压力的电解液射向工件表面,在加电状态下形成通路,利用电化学阳极溶解sicp/al复合材料中的铝合金基体,再通过流动的电解液带离脱落的sic和废液,结合界面逐步破坏,使sic颗粒剥离表面,从而完成整个加工过程 [23] 。因此该方法得到的表面粗糙度通常较高(图6)。
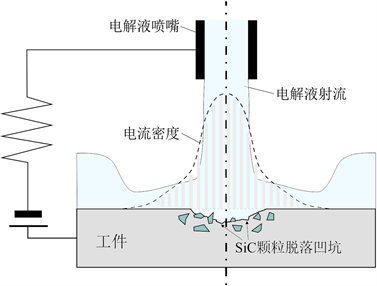
. schematic diagram of electrochemical jet processing
图6. 电化学射流加工示意图 [24]
刘壮等 [23] [24] 探讨了电化学射流加工和磨粒流加工的材料去除机理,分析了加工参数对加工形貌及材料去除率的影响。研究表明材料去除速率随加工电压的增加,加工过程主要包括铝基体的阳极溶解与sic颗粒的冲刷脱落,sic颗粒脱落后在加工表面直接形成微坑,对表面粗糙度具有较大影响。秦向阳 [25] 在对17 vol.% sicp/al进行电解加工时,发现nano3电解液的加工稳定性优于nacl,没有发生明显烧蚀现象,但会在材料表面形成钝化层,需要增大电流从而提高加工效率或通过加入sic磨粒以提高较小电流密度下的加工效率和加工质量。
与电火花加工和电弧放电加工能够产生局部高温不同,电解加工中的电化学蚀除作用仅能够作用于sicp/al复合材料中的铝合金基体上,对于低体分材料(≤25 vol.%)能够具有良好加工效果,而随着材料sic颗粒占比增加,导电性变差,脱落的增强体颗粒增多,一方面会导致蚀坑成片相连,严重影响表面粗糙度,另一方面会恶化电解环境,影响加工稳定性。因此单一电解加工不能满足中高体分sicp/al复合材料的加工应用。
3. sicp/al复合材料超声辅助加工技术
(一) 超声机械加工
目前,随着sicp/al复合材料应用领域的拓宽,应用超声波振动切割工艺加工sicp/al复合材料的趋势逐年增加,并且在sicp/al复合材料的制造中采用了超声振动复合多种机械加工技术。超声振动作用有效促进了材料微观缺陷的消除和晶界的再结晶,通过切削动作和刀具运动方向的周期性波动,使振动切削过程瞬间完成 [26] 。
河南理工大学向道辉团队 [27] [28] [29] 利用超声振动铣削加工了20%、55%和65%等体分的sicp/al复合材料,研究了刀具磨损机理、表面形貌特征、铣削参数对铣削力的影响,实验证明与传统铣削方法相比,降低了切削力、刀具磨损,有效地提高了刀具寿命。
超声加工相较于传统机械加工能够有效降低切削力,提高刀具使用寿命,获得良好的表面质量,且随着sic体积分数的增加,超声振动切削相对于传统加工的优势变得更加明显,但超声加工的加工面积较小,在加工大尺寸复杂结构件产品时具有局限性。
(二) 激光/超声辅助机械加工
将激光热场引入sicp/al复合材料的机械加工区域能够有效软化基体材料,降低颗粒与基体之间的界面结合强度,促进界面脱粘,从而使材料表面塌陷、空洞等缺陷明显减少,提高加工效率 [30] 。
胡茂顺 [31] 、彭培成 [32] 、赵国龙 [33] 等学者分别研究了sicp/al复合材料的激光加工和激光辅助加工(lam),这两种方法虽然可以显著提高材料的去除率,并在一定程度上降低刀具磨损,但由于激光的高能高温效应,导致工件加工精度和表面质量不高,还可能出现热裂纹等缺陷,因此不适合该种材料的精密加工。
激光辅助超声铣磨虽然能够及时排出切割区域的热量,增强材料的切割性能,但切削液不适用于激光辅助加工,如果激光功率过大,容易造成较大较深的热影响区,不能有效减少加工过程中的表面损伤,因此也限制了在复合材料中的广泛应用。
4. sicp/al复合材料复合加工技术
综上所述,机械铣削加工主要存在刀具磨损严重的问题,磨削加工可实现高表面质量和尺寸精度的加工,但难以实现复杂结构的加工;电火花加工常用于槽、孔等结构的加工,但加工效率低,很难实现表面精加工;而电解加工适合低体积分数的sicp/al复合材料的加工,不能很好的满足高体积分数材料的加工需求;而超声振动铣削与传统铣削方法相比,虽然降低了切削力和刀具磨损,在加工中高体分薄壁构件时反而容易造成崩边崩缺。
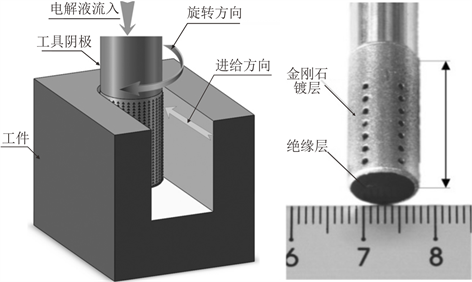
. schematic diagram of electrochemical milling-grinding and tool cathode photo
图7. 电解铣磨复合加工示意图及工具阴极照片 [34]
徐国梁等 [34] 对15 vol.% sicp/al复合材料进行了电解铣磨复合加工(ecgm),通过流场建模仿真,获得了流速分布均匀的工具阴极结构以保证电场的均匀分布,再在阴极基体表面镀金刚石磨粒和底部绝缘处理,最终实现了材料去除率为255.9 mm3/min,沟槽侧壁粗糙度值为ra1.933 μm的加工(图7)。
王系众等 [35] 针对薄壁零件的电解铣削加工,设计并制作了大直径工具阴极,研究了电压和进给速度对其加工效率和加工深度的影响。试验结果表明:提高加工电压能够提升材料去除率和加工深度,降低进给速度能够获得更大的加工深度;在40 v加工电压的参数下,单次进给的最大材料去除率达到了279.85 mm3/min,加工浅槽的最大深度达到了1.392 mm。
(一) 超声振动–电火花
针对传统电火花加工过程中放电性能不稳定、加工生产率低、表面一致性差等问题,超声振动电火花加工(uvg-edm)应运而生 [36] [37] ,相比单一电火花加工可将材料去除率提高30%以上,并且超声振动作用可以有效缓解短路放电和间隙放电时的集中放电现象,去除放电产生的电蚀凹坑凸边和拉弧烧伤,显著减少工具磨损。
超声振动电火花加工在sicp/al复合材料加工中的应用得到了较为广泛的研究,而如何选择合适的加工参数和加工策略以达到更好的工艺效果一直是加工中的重要问题。
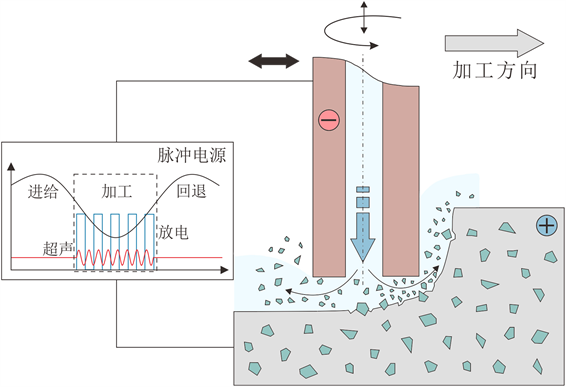
. ultrasonic-edm schematic diagram
图8. 超声–电火花复合加工示意图 [38]
房晓龙等 [38] 提出了一种超声振动断续式电火花加工方法(图8),在加工过程中,工具电极的快速振动使工作液产生极强的液压冲击,快速排出加工产物,减少能量消耗,提高加工效率,同时利用脱落的sic颗粒充当磨料,进一步提高加工表面质量。李护林等 [2] 在电火花成形机床sf201上加装超声波发生器和超声振动主轴(频率28.3 khz,振幅3 μm),采用优化后的电火花加工参数对sicp/al减重型孔的加工效率约为16.4 mm3/min,表面粗糙度约为ra0.8,重熔层及热影响区域为3 μm,进行单个型腔加工后的电极损耗为8.34%。孟涛等 [39] 通过超声振动磨削电火花复合加工52vol.% sicp/al的正交试验极差分析结果表明,影响表面粗糙度的因素由小到大依次为:电流 > 加工脉宽 > 弹簧预紧力 > 脉冲占比;复合加工放电波形分析结果表明,加工过程中主要为短路放电和间隙放电组合,同时,超声振动作用能够有效减少放电集中,促进消电离过程。李铠月等 [40] 将超声振动装置组合在edm jmdy-50ii精密电火花加工机床上,通过专用电极头,对30 vol.%工件进行超声磨削电火花复合加工;以电火花去除基体为主,磨削去除sic颗粒为辅,有效减弱了纯电火花加工时sic颗粒对放电过程的屏蔽作用,使加工持续进行,最终获得了粗糙度ra2μm加工表面。
(二) 电解–超声振动
电解–超声辅助磨削是建立在电解在线砂轮修整技术(elid)磨削工艺上的复合加工技术 [41] [42] ,是利用在线电解作用连续修整砂轮表面获得磨粒凸出,并借助不断产生的表面氧化物绝缘层达到动态平衡,再通过超声振动机构辅助提高材料去除率,最终实现可自适应控制的高质量磨削过程(图9)。
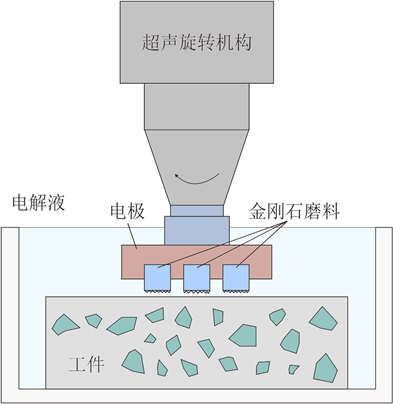
. the schematic diagram of ultrasonic assisted electrolytic composite machining [1]
图9. 超声辅助电解复合加工示意图 [1]
在超声电解复合加工过程中,超声高频振动、超声空化作用能够去除电解加工所产生的钝化膜,加速加工区电解液循环和电解产物的排出,进给提高加工效率,提高材料去除率,同时又能保持较好的加工精度和表面质量。南京航空航天大学云乃彰教授和扬州大学朱永伟教授等 [43] 对超声电解复合加工机理及技术优势进行了探讨,利用自行研制的变幅杆和不同截面的微细工具阴极开展了一系列超声电解复合微细加工基础试验研究,初步证实了这种复合技术的可行性和加工特点。
关佳亮等 [44] [45] 分别对40 vol.%和60 vol.% sicp/al进行了elid磨削加工试验并对加工设备和专用电解液做了大量研究,试验得到样件的表面粗糙度分别为95 nm和106 nm,得出加工参数对表面粗糙度的影响程度顺序为:加工深度 > 砂轮线速度 > 占空比 > 电解电流。杨光美等 [46] 选用matlab软件建立了超声振动磨削放电加工30 vol.% sicp/al的支持向量机预测模型,通过预测结果实现了优选的脉宽、脉间峰值电流、加工电压和电极振幅加工参数。
(三) 电解–电火花
电解–电火花复合加工常用于高温合金和硬脆材料加工,是集电化学、物理、机械等融合交叉的多场耦合作用下的复合加工技术 [47] 。在加工过程中,不仅有电化学阳极溶解、放电气化蚀除,还有机械辅助作用下的材料去除,与纯电火花加工不同,整个加工过程均在电解液中进行,因此电解液需要具备较低的浓度和电导率,以同时满足需要导电环境的电解加工和需要低电导率环境的电火花加工。
唐健等 [48] 对电解–电火花复合加工电极磨损机理进行了研究,实验结果表明随着工作液电导率的增加,相对电极损耗率逐渐降低;随着脉冲宽度增加,相对电极磨损率逐渐降低;峰值电流的减小也会使电极损耗降低;最终相比电火花高速穿孔加工电极损耗减少了14.7%。崔保伟等 [47] 开展电解–电火花加工涡轮静子试验,使用16%质量分数的nano3电解液,与单独采用电火花加工相比,加工效率提高52%,设备成本降低46%。魏志远 [49] 和王涛 [50] 将超声振动装置与电解–电火花加工设备相结合,形成了超声–电解–电火花复合加工,实现了难加工材料异形面结构和典型微结构的精密高效加工,如图10。
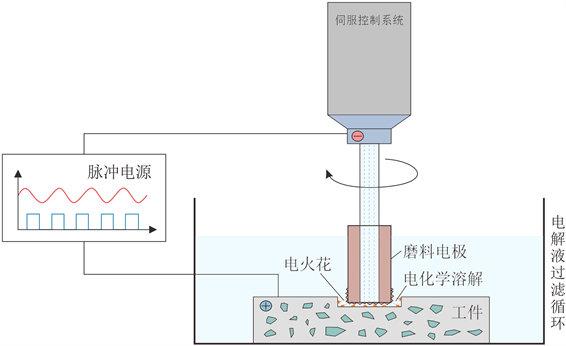
. electrolysis-edm schematic diagram
图10. 电解–电火花复合加工示意图
作为典型的难加工复合材料,电解–电火花复合加工技术也能够很好的运用在颗粒增强铝基碳化硅材料加工上,通过避开对高硬度sic颗粒的直接切削,进行大余量去除及薄壁、镂空、深孔等复杂结构的加工,最终形成高效、低应力、高精度的sicp/al复合材料复合加工方式(图11)。
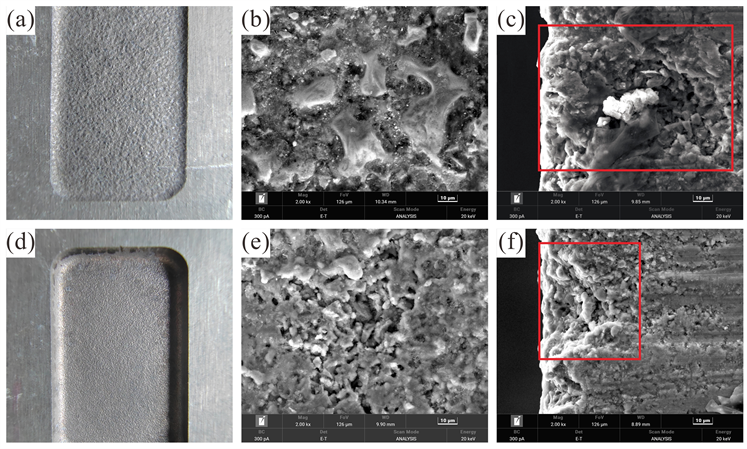
. the sicp/al composites surface morphology of electrolytic-edm composite machining; (a) high power electrolysis-edm surface; (b) sem characteristics of machined surface; (c) cross-sectional characteristics under the microscope; (d) low power electrolysis-edm surface; (e) sem characteristics of machined surface; (f) sem photos of machined surface
图11. 电解–电火花复合加工sicp/al复合材料表面形貌;(a) 高功率电解–电火花加工面;(b) 加工表面sem特征;(c) 加工截面sem照片;(d) 低功率电解-电火花加工面;(e) 加工表面sem特征;(f) 加工截面sem照片
5. sicp/al复合材料组合加工
针对航空航天难加工复杂结构零部件的高效、高质量的加工需求,在同一台加工中心上依次实现大余量去除加工方式和机械铣削等加工功能,粗加工时通过低应力电加工高效大余量去除,然后直接切换到高精度加工模式完成工件关键部位和表面的精加工 [51] 。
赵万生和康小明 [22] 以及刘晓等 [52] 介绍了高速电弧放电–机械铣削组合加工技术和机床设备,其兼具了传统数控加工功能和电弧放电加工的过程控制,进行了必要的防护和绝缘处理,实现了加工状态实时监测和放电间隙伺服控制;在加工时,先进行高能量高去除率加工,然后采用小能量电弧放电改善表面粗糙度和表面精度,从而在后续的铣削精加工时,能够获得刀具磨损小、加工状态稳定,加工变形量低的加工状态。
对sicp/al坯料通过高功率电弧加工进行大余量高效去除后,配合去应力退火处理改善后续加工性,防止材料出现变形开裂等问题;在此基础上,降低电弧放电功率进行半精加工,最后通过高精度数铣加工完成产品的加工流程。通过对电弧加工工装的多次改进和工艺方案的不断优化,经过多次试验验证,电弧加工相比传统加工工艺效率提升了2倍以上,起到了良好的降本增效作用(图12)。
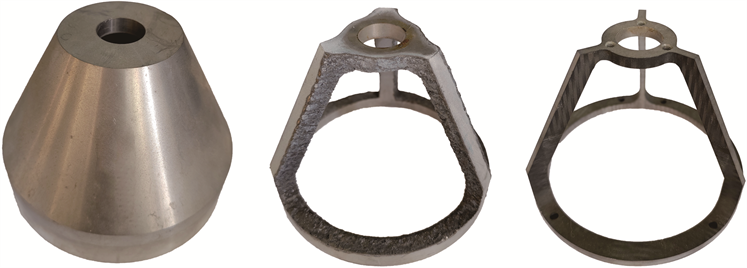
. arc discharge-mechanical milling combined machining process of sicp/al structural parts; (left) blank material; (medium) high power arc discharge rough machining; (right) low arc discharge semi-finishing and digital milling machining
图12. sicp/al结构件电弧放电-机械铣削组合加工过程;(左) 坯料;(中) 高功率电弧放电粗加工;(右) 低电弧放电半精加工和数铣加工
6. 结论
近年来,随着武器装备和航空航天领域的高速高质量发展,对sicp/al等典型的高强度难切削材料的加工制造也提出了越来越高的要求:一是航空航天结构件的加工尺寸精度和表面质量要求越来越高,成本控制越来越严格;二是随着武器装备的不断升级换代和先进材料在航空航天制造中的应用越来越广泛,需要更短的交付周期;三是加工设备的自动化、智能化趋势越来越显著,需要更为系统全面的凯发娱乐官网的解决方案;因此,也更加急迫需要对这类材料的高效高精度加工技术和相关设备的创新研究。
1、传统机械加工和单一模式的电加工等手段均难以克服sicp/al复合材料的难加工特点,无法满足航空航天产品的高品质要求。需要在电解、电火花、超声、机械铣磨等主流加工方法中进行两种甚至两种以上加工方法相复合的思路,在此基础上进行加工设备和装置的改进、复合加工机理研究以及加工仿真模拟等方面的深入探索。
2、超声复合电火花加工方法能够加工出具有较好表面粗糙度且重熔层和热影响区域小的槽、孔和型腔结构,但面对大余量去除的情况时,其加工效率远低于电解加工与超声铣磨加工;电解–铣磨加工能够达到较高材料去除率和优良表面粗糙度,与常用的超声铣磨加工在加工效率方面相当,但超声铣磨也同样具有机械加工时的刀具磨损、加工应力以及加工区域局限性等问题;电解–电火花复合加工可以在sicp/al复合材料表面交替产生电解和电火花作用,结合高可靠控制系统并搭配合理工艺参数能够实现高效高质量复合加工。
3、建立在高可靠控制系统的基础上,使用同一台加工设备上进行两种以上加工方式的组合加工。再与传统加工方式进行精密高效整合,能够大大缩短产品制造周期,降低加工成本,提高加工质量,已成为sicp/al复合材料加工技术新的重要发展方向。